The first task is to set "Top Dead Center" (TDC) on the engine. This is the point at which #1
piston is at the top of its travel up and down the cylinder bore.
Because the piston has a slight 'dwell' at its highest point ... it is important to find TDC very accurately as it will have a huge effect on
the rest of the camshaft
timing process if it is wrong. Fit the crankshaft cam sprocket to the crankshaft and locate on the keyway. Fit the protractor to the crankshaft
pulley and fit the pointer to the front cover bolt hole as shown above. The dead stop shown above
is bolted accross the cylinder face of the block and the central bolt adjusted so that it is clear of the piston crown, allowing the engine to
be fully rotated.
Turn the engine until the piston appears to be at the top of its travel .... then rotate the engine aproximately 20 degrees anti clockwise.
Now carefully adjust the
central bolt of the dead stop until it touches the piston. Rotate the protractor until TDC is aligned with the pointer. Now rotate the engine
slowly anti clockwise until the piston comes beack up the bore and again touches the dead stop bolt. Note the angle of the protractor.
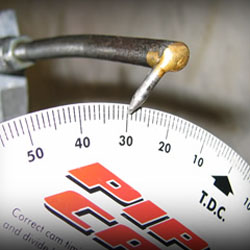
Whatever the value of this protracor reading (in the picture 30 degrees), halve that value (in this case 15 degrees) and adjust the protractor to align 15 degrees with the
pointer. Now rotate the engine clockwise until the central bolt again touches the piston. Check the protractor, the value should now be 15 degrees on the other side
of TDC. If it is, you have set TDC. If it is not ... adjust the bolt slightly looser ... and repeat the process until you have an equal number of degrees either side
of the TDC mark on the protractor (without moving the central bolt). Once you are happy that it is set, DO NOT MOVE THE POTRACTOR! until you have finished setting the
camsaft timing.
The next step is to fit the camshaft (if it is a fully adjustable timing chain set you will need to approximate the initial alignment)
and a follower into #1 inlet gallery, this is the front gallery on the right hand side,
it is best to use a solid follower, but if you dont have one, just make sure that the follower you use is not really loose on the inner plunger, or you could get strange readings.
Now fit the DTi, the engine is aluminium, so if you use a magnetic based dti, you will need to bolt a steel plate somewhere to mount it.
Then align the dti so that its pointer is in the centre of the follower in #1 inlet valve's camshaft follower. Check that it is central and does not 'ride up' the follower dish as
the pointers arm moves.
We are now ready to begin timing the cam in. It is really important that from now on, you only take measurements whilst rotating the engine in a
clockwise direction, this is to eliminate any slack in the timing chain. Rotate the camshaft until the protractor reads 100 degrees before TDC
Now set the dti to 0 on its rotating bezel. This is now our first reference point. Now slowly rotate the engine clockwise whilst watching the dti carefully.
The pointer should move away from 0 mark ... then come back to it. When it arrives back at 0 ... read the number of degrees from the protractor ...
In the example above it shows 118 degrees. So now we need to do a little maths! Take 100 from the number of degrees, halve the result, and add 100 back on:
118 -100 = 18
18 / 2 = 9
9 + 100 = 109
Making the cam timing value 109 degrees.
Obviously ... if this is the correct timing for your cam ... just re-check by repeating the entire timing procedure ... if not, then adjust and repeat until it does.
Remembering to only measure when turning clockwise.